

To get the most work out of the steam, the exhaust pressure is kept very low. The steam entering the turbine is at 306 ☌ and 6.32 bar. From the intermediate pressure turbine, the steam continues its expansion in the three Low pressure turbines. On leaving the boiler reheater, steam enters the intermediate pressure turbine at 565 ☌ and 40.2 bar pressure. The exhaust steam from this section is returned to the boiler for reheating before being used. The high pressure steam at 565 ☌ and 156 bar pressure passes through the high pressure turbine. Any improvement in the design of steam turbine enables more efficient use of fuel and results in reduced cost. The steam turbine unit largely influences the efficiency and reliability of power stations. Siemens Power Generation, for example, has improved the overall efficiency and availability of its steam turbines by decreasing the steam flow energy losses in each of the steam turbines components. During the last several years the primary changes to the design of steam turbines have focused on improving their efficiency, reliability and reducing operating costs. The work involves design considerations, design checks, validation and sensitivity analysis to achieve the design criteria to fulfill the structural requirements for mechanical integrity. In the present work, one such analysis is carried out blending the hand calculations and steady-state finite element analysis to evaluate the contact pressure in a high pressure steam turbine casing. Our industrial wastewater solutions help you minimize environmental impact and ensure compliance with permits.Contact pressure and pretension in bolts-analysis has been made easier in recent years due to the availability of high computational capabilities and flexibility in the computational methods using finite element analysis. Industrial wastewaterĮnsure compliance with all discharge requirements. Cooling waterĮnsure heat transfer processes are as efficient as possible by effectively controlling total suspended solids (TSS) to avoid the expense and downtime associated with fouling and mineral buildup that can cause scaling and hazardous operating conditions.
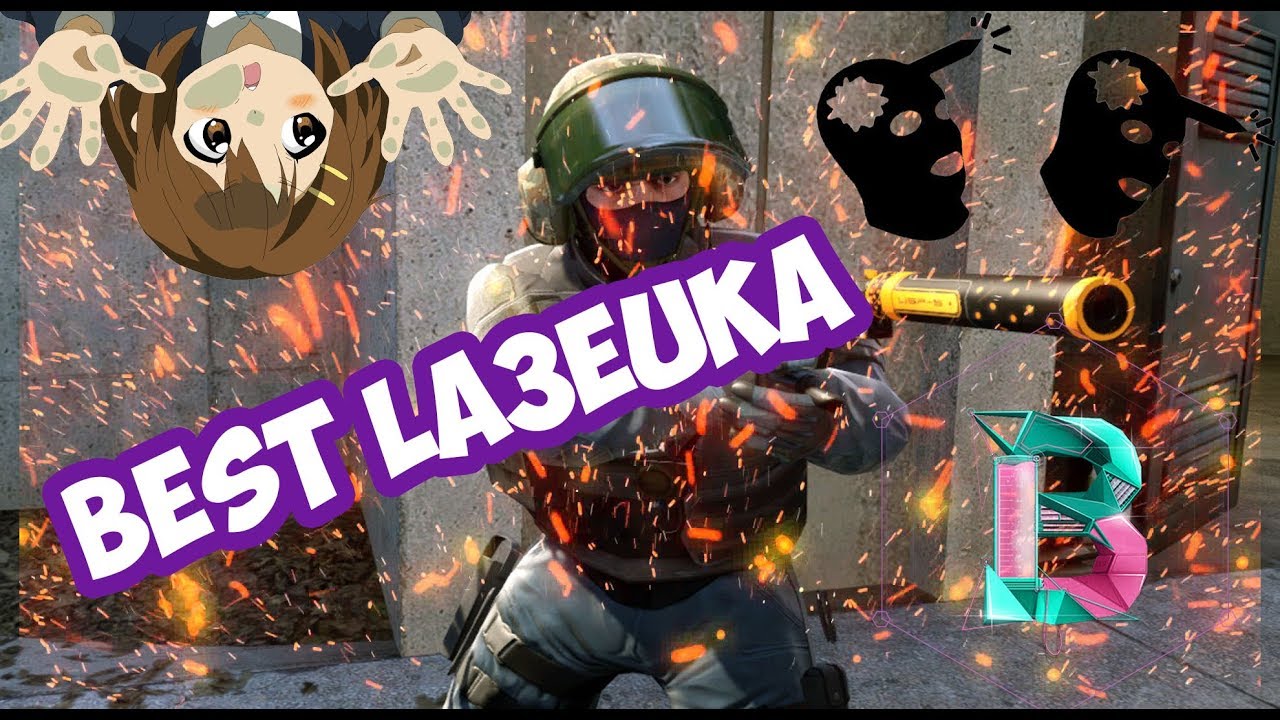
Minimize silica levels to prevent turbine blade erosion, and monitor and manage dissolved oxygen (DO) to prevent corrosion. Protect your equipment – from pipes and tubes, to turbines and boilers – by ensuring your water is of the highest quality. By properly treating water at this stage, you can reduce costs and treatment within the power and steam generating process. Proper influent water monitoring is the first defense to protecting the health of your equipment and preventing corrosion. Pretreat influent water before it enters your plant’s system.
#Steam anylist verification#
We offer the field equipment and industry expertise to minimize monthly power plant maintenance while holding true to both water quality requirements and verification protocols, which can help you improve the thermal efficiency of steam power plants and increase uptime.įeatured Applications for the Power Generation Industry Influent water treatment With less labor, narrower error ranges, more accurate results, Hach provides trusted measurements to assist power stations and their water management partners as they strive to improve efficiency in within all areas of your power plant. With our laboratory, online, portable, and on-site solutions, we help you protect against power plant water pollution, contamination, corrosion, scaling, and fouling, and ultimately, keep your workers, operators, and equipment safe. Our reliable and accurate solutions for ultrapure, pure, and non-pure water parameters serve the diverse needs of fossil power plants, nuclear power plants, cogeneration, and heat and steam production. We offer the most comprehensive suite of water solutions for the power generation industry, helping you reach, improve, and maintain your efficiency goals. In short, with Hach, you get results that are consistent, verifiable, and powerful. For more than 85 years, we’ve led the way in water quality analysis, delivering an expertise you can rely on for water system monitoring, verification, and protection that keeps your plant online and efficient.įor decades, the power generation industry has turned to Hach for expert solutions and support-from purification to power plant pollution prevention, Steam and Water Analysis Systems (SWAS) to process monitoring and laboratory verification. Hach ® understands the critical role water plays in power plant efficiency and, ultimately, profitability.
